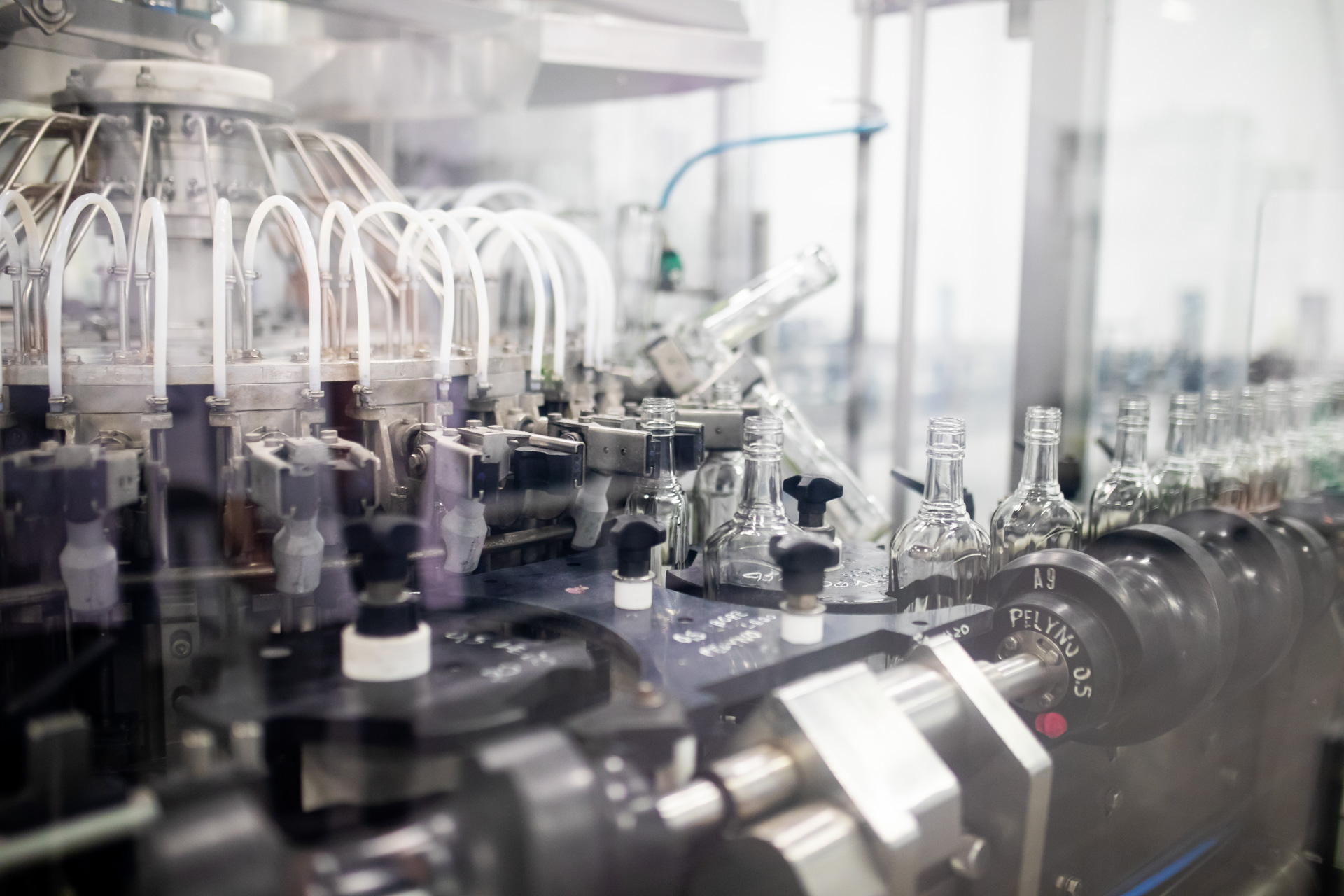
The energy resources (consumption) monitoring system is one of the recent innovations in the MV GROUP Production organisation. The system is already in operation at the company’s Alita beverage factory and the experience gained there will be applied to achieve greater energy efficiency and sustainability at the Anykščių vyno, Stumbras and Gubernija factories. The monitoring data is analysed by the company’s team and translated into solutions that create value for the environment and business.
According to Gediminas Puodžiūnas, Head of Engineering at MV GROUP Production, working with data is the foundation of technological progress. That’s why MV GROUP Production, a beverage manufacturing company, is deploying systems that collect and process a wide range of data on energy consumption. This allows professionals to discover ways to better manage and conserve resources.
Careful preparation helps to avoid irrational spending. Innovations are only introduced after a careful assessment of their suitability and potential to bring about real change and benefits, and this preparation period not only brings teams together on common tasks and clarifies responsibilities, but also allows them to see the bigger picture.
“Each MV GROUP Production factory is like an organism, made up of different technological and engineering systems and processes. A detailed analysis is needed to understand the specificities of each of these “ecosystems” and their impact on energy intensity. By analysing the data, we can discover certain regularities between energy consumption and the technological and ancillary processes. We can then pinpoint locations and define ways to improve energy efficiency and sustainability,” explains G. Puodžiūnas.
There is a clear plan
Monitoring systems are not new in manufacturing companies, but modern solutions are far more advanced than systems that are 10-15 years old. “In other words, today’s technology allows us to hit the target faster and more accurately – saving resources and significantly increasing productivity at every step of the process,” says Puodžiūnas. As a result, investments pay off faster and changes have a greater impact.
An important outcome of MV GROUP Production’s preparation work is a detailed plan for how the monitoring system will be gradually implemented and developed. It is common practice in the company that progress is not only about technology, but also about employees, providing them with new opportunities to improve their skills and knowledge.
“Our common goal is simple – a successful, sustainable organisation that produces competitive and high-quality products that represent Lithuania worldwide. Each of us contributes to this success. So, by opening our minds to innovation, we open a wider path to success,” says G. Puodžiūnas, Head of Engineering.
Where to start to save more?
He says that the development of an energy monitoring system should start with three main steps: identification of energy-intensive sites and processes; deployment of the monitoring system elements at the identified points; and analysis of indicators. It is in these steps that a company opens a cycle of continuous improvement: once the data has been collected, solutions are developed and implemented, then their effect is analysed, etc.
Currently, specialists are analysing data from ancillary processes such as ventilation, cooling, heating, lighting, etc. At the same time, data on energy consumption in production and technological processes are being analysed. The new monitoring system at the Alita factory collects the information for analysis.
The analysis will lead to the definition of certain energy consumption patterns and “habits”. Data analysts will then “drill down” to even finer indicators that reveal the costs of both process and supporting processes.
In this way, step by step, first Alita and then other MV GROUP Production beverage factories will follow a path of energy efficiency based on data science. Other projects to improve sustainability will be developed in parallel.
Fosters defined expectations
By having an energy consumption monitoring system in place and working with it properly, the company’s team of experts hopes that it will help to identify faults and equipment malfunctions more quickly. It has been repeatedly observed that poorly functioning equipment leads to higher resource consumption. Or, conversely, if costs are abnormally low, this may also signal problems.
“Poorly functioning equipment can be fixed, tuned up. But it can also be the case that it simply needs to be replaced – an investment is needed. This means that the monitoring system helps to anticipate and better manage investments,” shares G. Puodžiūnas.
He adds that the system helps to identify excessive requirements sometimes applied in processes and to optimise the implementation of norms.
More environmentally friendly solutions
Summarising the changes, the Head of Engineering says that the initial investment in the monitoring system and metering points at the Alita factory is like a journey into the depths of data. Once this step has been taken, it will be decided how to further develop the system and where and how many new metering points to install. All this will determine the next stage of investment and the way forward towards greater sustainability.
The experience gained in Alytus will also be very useful for the implementation of monitoring systems at Anykščių Vynas, Stumbras and Gubernija factories, where decisions can be made more quickly and efficiently.
Puodžiūnas admits that his favourite feeling is when he and his team come to significant conclusions and discoveries. This is what can be used to further underpin effective solutions and to achieve tangible breakthroughs in sustainability.
“It is important that MV GROUP Production pursues progress systematically and broadly. New energy projects are being developed and implemented – from solar power plants on the roofs of buildings, to the replacement or modernisation of process lines, to the control of processes inside factories. In the long term, all this should yield good results, both financially and environmentally,” says the company’s Head of Engineering.